Silicij nitrid (Si₃N4) keramika, kao napredna konstrukcijska keramika, posjeduje izvrsna svojstva kao što su otpornost na visoke temperature, visoka čvrstoća, visoka žilavost, visoka tvrdoća, otpornost na puzanje, otpornost na oksidaciju i otpornost na trošenje. Osim toga, nude dobru otpornost na toplinske udare, dielektrična svojstva, visoku toplinsku vodljivost i izvrsne performanse prijenosa visokofrekventnih elektromagnetskih valova. Ova izvanredna sveobuhvatna svojstva čine ih naširoko korištenim u složenim strukturnim komponentama, posebno u zrakoplovstvu i drugim područjima visoke tehnologije.
Međutim, Si₃N4, budući da je spoj s jakim kovalentnim vezama, ima stabilnu strukturu koja otežava sinteriranje do visoke gustoće samo difuzijom u čvrstom stanju. Kako bi se pospješilo sinteriranje, dodaju se pomoćna sredstva za sinteriranje, kao što su metalni oksidi (MgO, CaO, Al₂O₃) i oksidi rijetkih zemalja (Yb₂O3, Y₂O₃, Lu₂O₃, CeO₂), kako bi se olakšalo zgušnjavanje putem mehanizma sinteriranja u tekućoj fazi.
Trenutno globalna tehnologija poluvodičkih uređaja napreduje prema višim naponima, većim strujama i većoj gustoći snage. Istraživanje metoda za izradu Si₃N4 keramike je opsežno. Ovaj članak predstavlja procese sinteriranja koji učinkovito poboljšavaju gustoću i sveobuhvatna mehanička svojstva keramike od silicijevog nitrida.
Uobičajene metode sinteriranja Si₃N₄ keramike
Usporedba performansi Si₃N₄ keramike pripremljene različitim metodama sinteriranja
1. Reaktivno sinteriranje (RS):Reaktivno sinteriranje bila je prva metoda korištena za industrijsku pripremu Si₃N4 keramike. Jednostavan je, isplativ i može oblikovati složene oblike. Međutim, ima dug ciklus proizvodnje, što ne pogoduje proizvodnji u industrijskim razmjerima.
2. Sinteriranje bez pritiska (PLS):Ovo je najosnovniji i najjednostavniji postupak sinteriranja. Međutim, zahtijeva visokokvalitetne sirovine Si₃N₄ i često rezultira keramikom manje gustoće, značajnim skupljanjem i sklonošću pucanju ili deformaciji.
3. Sinteriranje vrućim prešanjem (HP):Primjena jednoosnog mehaničkog tlaka povećava pokretačku silu za sinteriranje, omogućujući proizvodnju guste keramike na temperaturama 100-200°C nižim od onih koje se koriste u sinteriranju bez pritiska. Ova metoda se obično koristi za izradu relativno jednostavne keramike u obliku bloka, ali je teško zadovoljiti zahtjeve debljine i oblika za materijale supstrata.
4. Sinteriranje plazmom iskre (SPS):SPS karakterizira brzo sinteriranje, usitnjavanje zrna i smanjene temperature sinteriranja. Međutim, SPS zahtijeva značajna ulaganja u opremu, a priprema Si₃N4 keramike visoke toplinske vodljivosti pomoću SPS još je u eksperimentalnoj fazi i još nije industrijalizirana.
5. Sinteriranje pod tlakom plina (GPS):Primjenom tlaka plina, ova metoda sprječava razgradnju keramike i gubitak težine na visokim temperaturama. Lakša je proizvodnja keramike visoke gustoće i omogućuje serijsku proizvodnju. Međutim, proces sinteriranja pod pritiskom plina u jednom koraku teško je proizvesti strukturne komponente ujednačene unutarnje i vanjske boje i strukture. Korištenje procesa sinteriranja u dva ili više koraka može značajno smanjiti intergranularni sadržaj kisika, poboljšati toplinsku vodljivost i poboljšati ukupna svojstva.
Međutim, visoka temperatura sinteriranja dvostupanjskog sinteriranja pod tlakom plina dovela je do toga da se prethodna istraživanja uglavnom usredotoče na pripremu Si₃N4 keramičkih podloga visoke toplinske vodljivosti i čvrstoće na savijanje na sobnoj temperaturi. Istraživanja Si₃N4 keramike sa sveobuhvatnim mehaničkim svojstvima i mehaničkim svojstvima pri visokim temperaturama relativno su ograničena.
Dvostupanjska metoda sinteriranja pod tlakom plina za Si₃N4
Yang Zhou i kolege s Tehnološkog sveučilišta u Chongqingu koristili su pomoćni sustav sinteriranja od 5 wt.% Yb₂O3 + 5 wt.% Al₂O3 za pripremu Si₃N₄ keramike korištenjem jednostupanjskog i dvostupanjskog procesa sinteriranja pod pritiskom plina na 1800°C. Keramika Si₃N₄ proizvedena postupkom sinteriranja u dva koraka imala je veću gustoću i bolja sveobuhvatna mehanička svojstva. Slijedi sažetak učinaka jednostupanjskih i dvostupanjskih procesa sinteriranja pod tlakom plina na mikrostrukturu i mehanička svojstva keramičkih komponenti Si₃N₄.
Gustoća Proces zgušnjavanja Si₃N4 obično uključuje tri faze, s preklapanjem između faza. Prva faza, preraspodjela čestica, i druga faza, otapanje-taloženje, najkritičnije su faze za zgušnjavanje. Dovoljno vrijeme reakcije u ovim fazama značajno poboljšava gustoću uzorka. Kada je temperatura prethodnog sinteriranja za proces sinteriranja u dva koraka postavljena na 1600°C, zrnca β-Si₃N₄ formiraju okvir i stvaraju zatvorene pore. Nakon prethodnog sinteriranja, daljnje zagrijavanje pod visokom temperaturom i tlakom dušika potiče protok tekuće faze i punjenje, što pomaže u uklanjanju zatvorenih pora, dodatno poboljšavajući gustoću Si₃N₄ keramike. Stoga uzorci proizvedeni postupkom sinteriranja u dva koraka pokazuju veću gustoću i relativnu gustoću od onih proizvedenih sinteriranjem u jednom koraku.
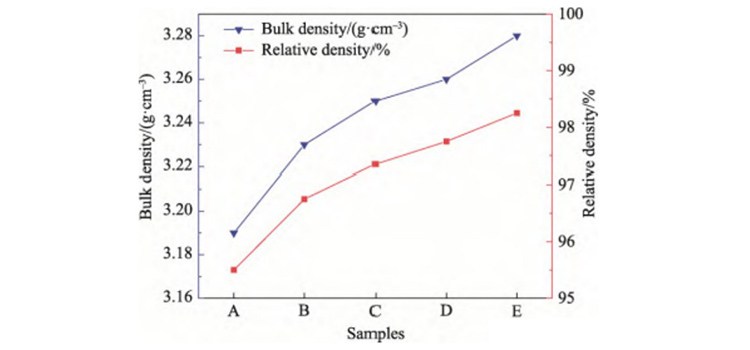
Faza i mikrostruktura Tijekom sinteriranja u jednom koraku, vrijeme dostupno za preraspodjelu čestica i difuziju na granicama zrna je ograničeno. U procesu sinteriranja u dva koraka, prvi korak se provodi na niskoj temperaturi i niskom tlaku plina, što produljuje vrijeme preraspodjele čestica i rezultira većim zrncima. Temperatura se zatim povećava do stupnja visoke temperature, gdje zrna nastavljaju rasti kroz Ostwaldov proces sazrijevanja, dajući Si₃N₄ keramiku visoke gustoće.
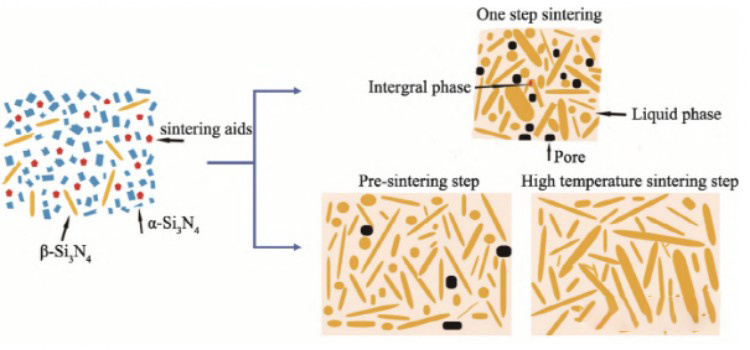
Mehanička svojstva Omekšavanje intergranularne faze na visokim temperaturama primarni je razlog smanjene čvrstoće. Kod sinteriranja u jednom koraku, abnormalni rast zrna stvara male pore između zrna, što sprječava značajno poboljšanje čvrstoće na visokim temperaturama. Međutim, u procesu sinteriranja u dva koraka, staklena faza, ravnomjerno raspoređena na granicama zrna, i zrna jednolike veličine povećavaju međuzrnastu čvrstoću, što rezultira većom čvrstoćom na savijanje pri visokim temperaturama.
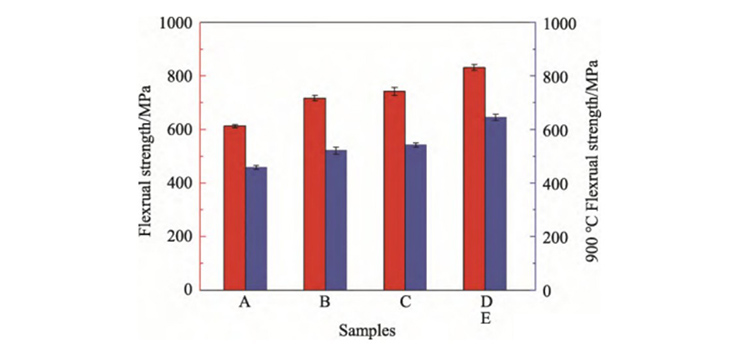
Zaključno, produljeno držanje tijekom sinteriranja u jednom koraku može učinkovito smanjiti unutarnju poroznost i postići ujednačenu unutarnju boju i strukturu, ali može dovesti do abnormalnog rasta zrna, što degradira određena mehanička svojstva. Korištenjem procesa sinteriranja u dva koraka—upotrebom prethodnog sinteriranja na niskoj temperaturi za produljenje vremena preraspodjele čestica i držanja na visokoj temperaturi za promicanje ravnomjernog rasta zrna— Si₃N₄ keramika s relativnom gustoćom od 98,25%, ujednačenom mikrostrukturom i izvrsnim sveobuhvatnim mehaničkim svojstvima može se uspješno pripremiti.
Ime | Podloga | Sastav epitaksijalnog sloja | Epitaksijalni postupak | Epitaksijalni medij |
Silicijski homoepitaksijalni | Si | Si | Epitaksija parne faze (VPE) | SiCl4+H2 |
Silicijski heteroepitaksijalni | Safir ili spinel | Si | Epitaksija parne faze (VPE) | SiH4+H2 |
GaAs homoepitaksijalni | GaAs | GaAs GaAs | Epitaksija parne faze (VPE) | AsCl3+Ga+H2 (Ar) |
GaAs | GaAs GaAs | Molekularna epitaksija (MBE) | Ga+As | |
GaAs heteroepitaksijalni | GaAs GaAs | GaAlAs/GaAs/GaAlAs | Epitaksija u tekućoj fazi (LPE) Parna faza (VPE) | Ga+Al+CaAs+ H2 Ga+AsH3+PH3+CH1+H2 |
GaP homoepitaksijalni | GaP | GaP(GaP;N) | Epitaksija u tekućoj fazi (LPE) Epitaksija u tekućoj fazi (LPE) | Ga+GaP+H2+(NH3) Ga+GaAs+GaP+NH3 |
Superrešetka | GaAs | GaAlAs/GaAs (ciklus) | Molekularna epitaksija (MBE) MOCVD | Ca, As, Al GaR3+AlR3+AsH3+H2 |
InP homoepitaksijalni | InP | InP | Epitaksija parne faze (VPE) Epitaksija u tekućoj fazi (LPE) | PCl3+In+H2 In+InAs+GaAs+InP+H₂ |
Si/GaAs epitaksija | Si | GaAs | Molekularna epitaksija (MBE) MOGVD | Ga、As GaR3+AsH3+H2 |
Vrijeme objave: 24. prosinca 2024